『タレントの時代』『トヨタの強さの秘密』と The Secret Behind the Success of Toyota
2015年に『タレントの時代』2016年に『トヨタの強さの秘密』を日本国内で、2018年に英語版”The Secret Behind the Success of Toyota” を世界で発売して以来、国内外多くの読者に恵まれました。同時に、日本を代表するグローバル企業であるトヨタの儲ける仕組みが実はほとんど世に知られていなかったことが分かりました。中でもトヨタ本体の中核機能であるトヨタ製品開発TPD(Toyota Product Development)すなわち「主査制度にもとづく新製品開発」の仕組みは、実は国内外で誰も正しく説明してきていませんでした。欧米で1990年代にトヨタ製品開発を調査した先駆者で、すでに他界したAllen Wardの仕事仲間で、リーン開発に関する著書のあるMichael Kennedyらは下記のように述べています。
GET STARTED NOW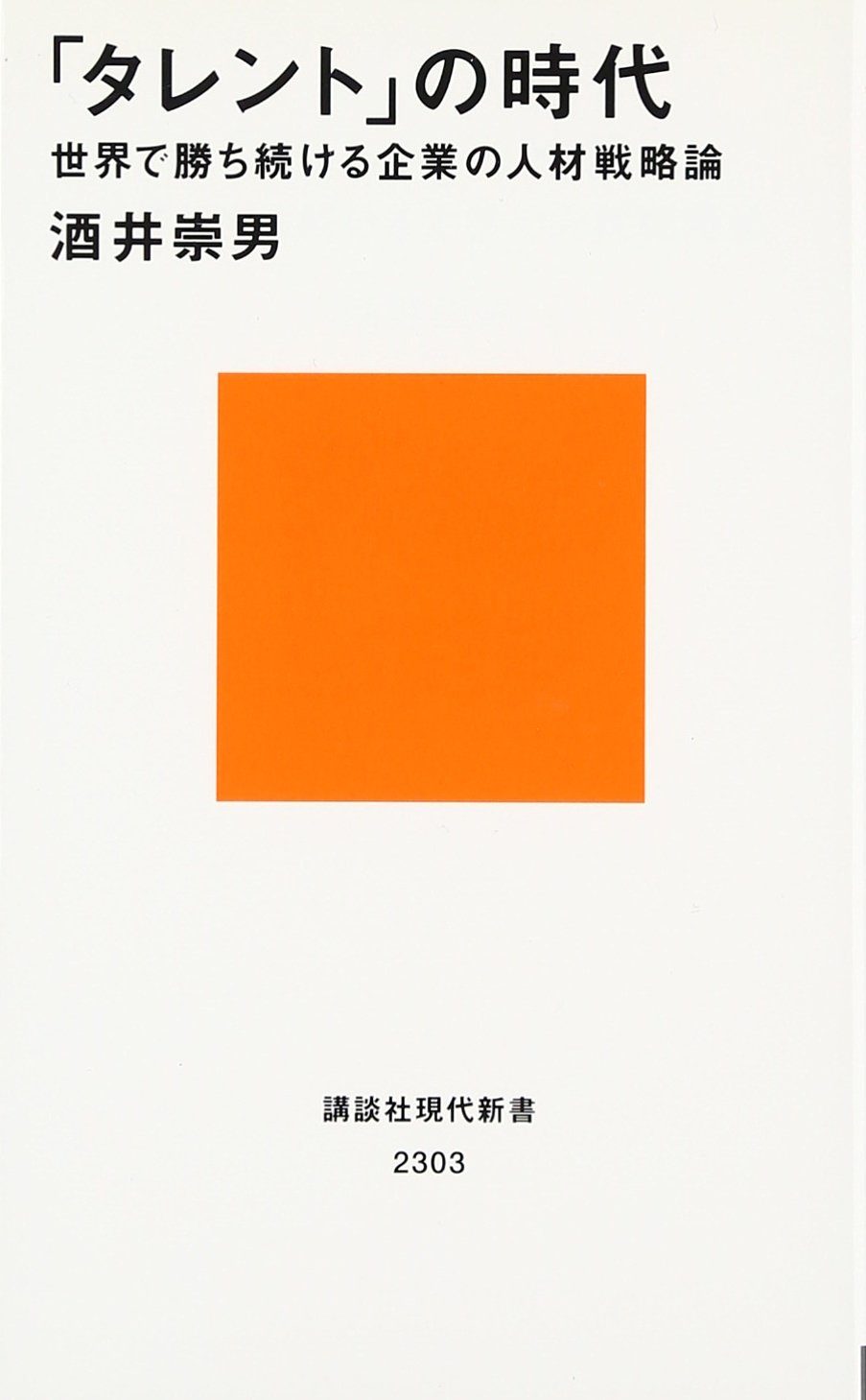
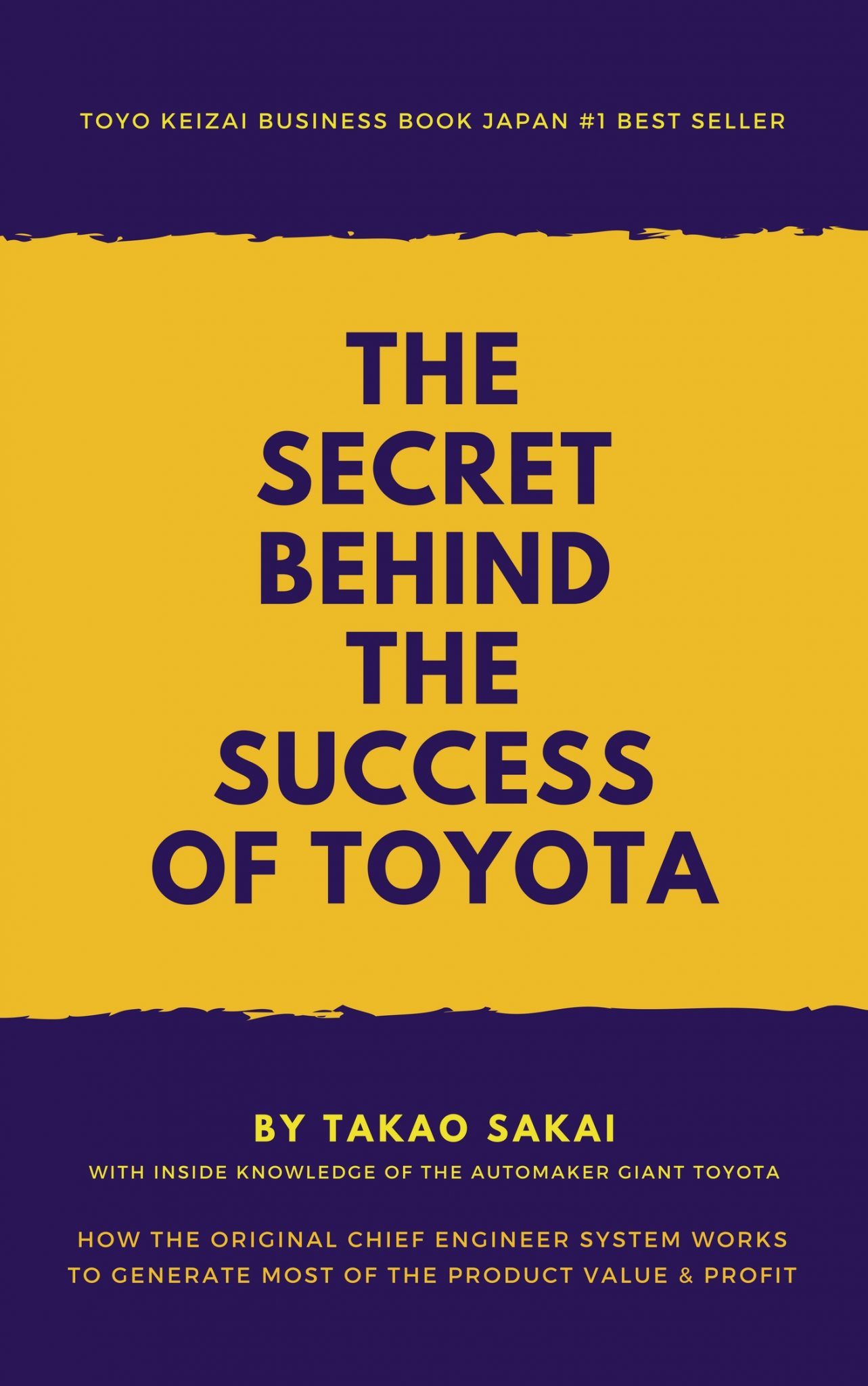
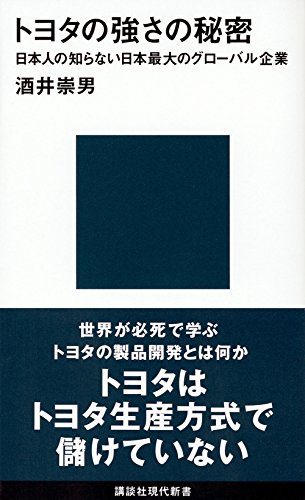
「欧米ではトヨタの製品開発手法を真似て多くの人達が主査(Shusaという英語になっている)やチーフエンジニアを中心とした、売れて利益が出せるプロダクト開発を目指してきたが、酒井さんが正しい解説を著書で展開するまでは、実際は誰もどういうものなのかよく理解していなかった」 こうした経緯で、いま欧米ではこの理解の遅れを取り戻す動きが始まっています。欧米ではアカデミズムもこの分野では大きく遅れをとっています。また主に欧米ものの著述の翻訳をしている日本の大学関係者は、さらに周回遅れに遅れているのが現状。最近では、欧米人が誤解した考え方・手法が製造業から他業界へヨコテンされ、それが日本国内に機械的に翻訳をされて逆輸入されてきています。 ここで重要なことは、字面だけ翻訳されてhow to 情報のみがインバウンドで日本国内へと入ってくる際に、一番重要なリーンの「目的・背景・文脈 」が大きく損なわれていることです。表面的な手続きの模倣に終始「なんの目的で○○をしているのか」などというおかしな議論が国内は見られます。中にはなんのことを言っているのか意味すら失われているものの解釈論議に終始しているような本末転倒な光景を目にします。
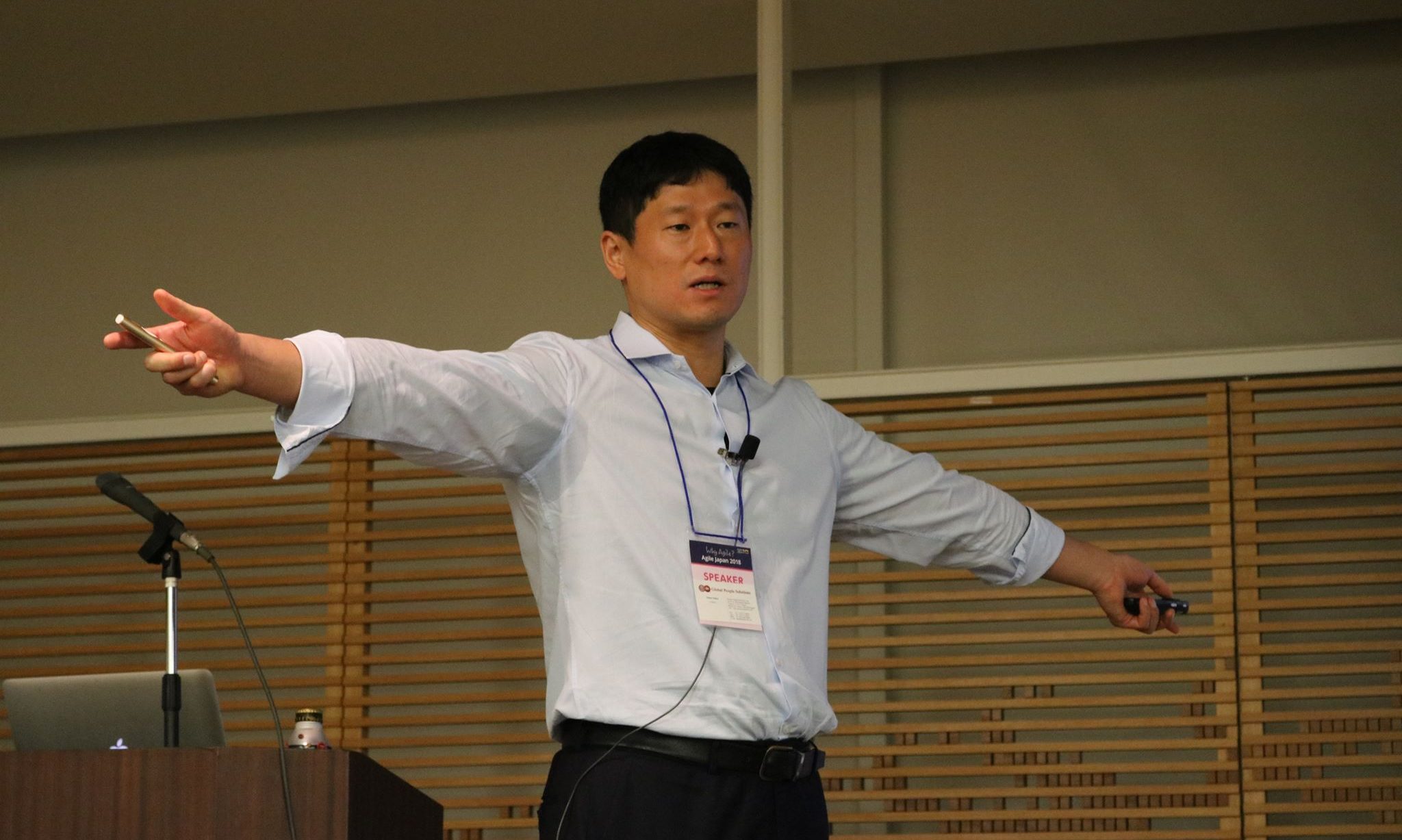
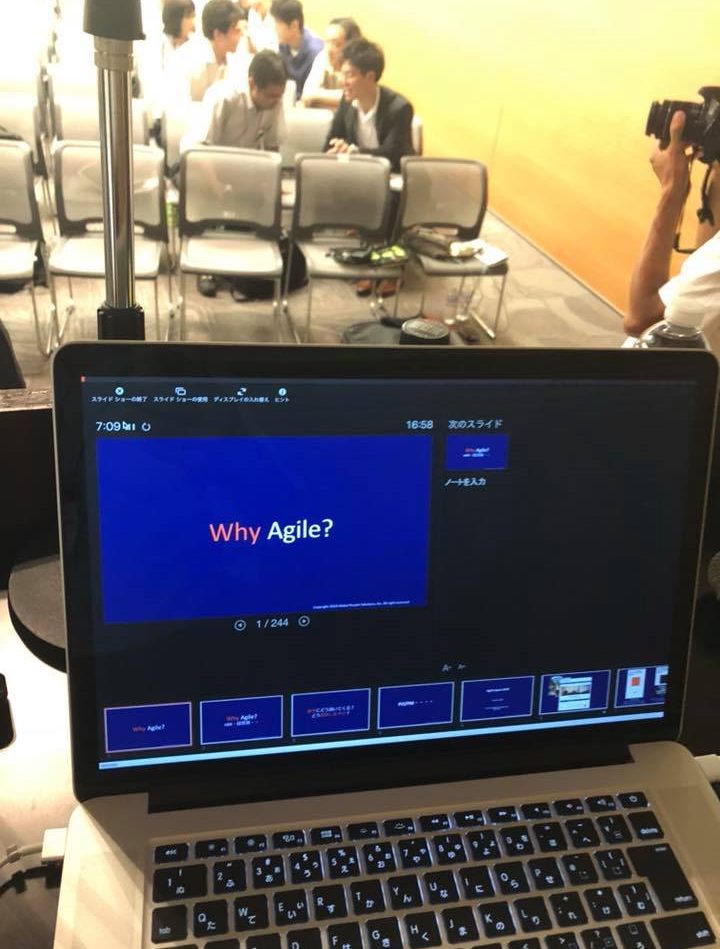
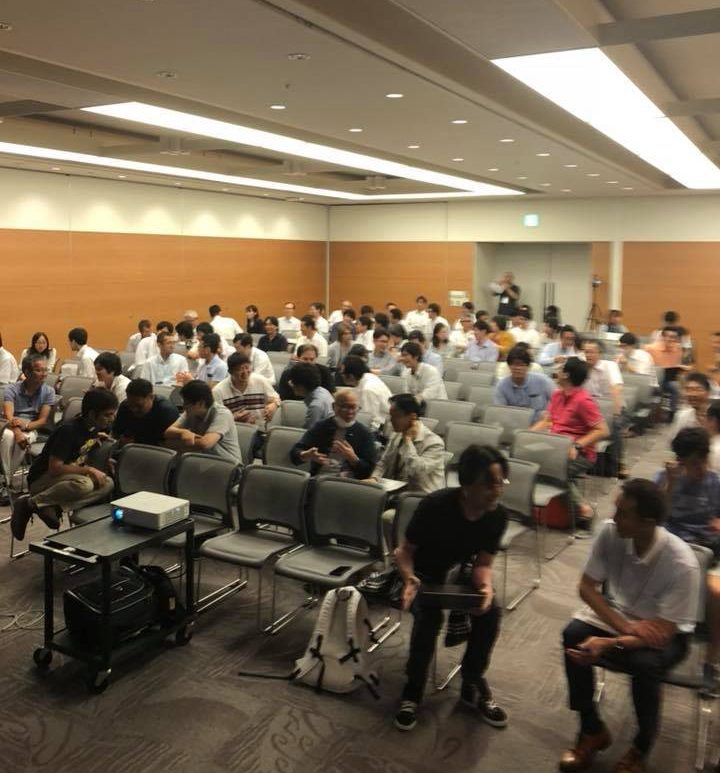
Agile・Lean の源流と課題
昨今流行しているソフトウエアリーン・アジャイル手法のひとつ「スクラム」もその典型と言えるでしょう。欧米人の理解したトヨタは量産工程のTPS+Gemba QC。量産工程のノウハウ派生では当たり前ですが、プロダクト開発やビジネスにまつわる問題は解決できません。量産工程リーンの派生手法で解決できるのは製造プロセスしか社内に持たない受託産業のみ。既存のアジャイル手法の多くは製造受託・社内受託・下請業務を目的としたものです。TPS・QCサークルや多能工のソフトウエア版は、現場のモラールの向上には多大に貢献し、協力し合う組織文化を醸成するという良い点はあります。しかしながら、顧客が満足するプロダクトや売上・利益に本質的には関係するものではありません。
例えば、スクラムフレームワークではサザーランドの言うToyota Shusa 派生のPO(Product owner)の役割が迷子になっており、ビジネス価値・プロダクト創造価値など経営の数字とつながる文脈が一切含まれていません。欧米のリーン業界のグル達も最近ようやく学習が始まりました。
欧米人の誤解を源流から正す。石川・朝香・デミングの本来の意図へも遡る
グローバル化・知識化し、TPSや生産技術など量産プロセスのノウハウが世界で知られ、工場の製造品質ではプロダクトの価値に本質的に差がつかなくなった現在、もちろん企画の質・設計品質で勝負する時代です。十分売れて十分利益の出るプロダクトを継続的に生み出す仕組みTPDを知っているか知らないかで勝負が決まります。W. Edwards Demingから石川馨・朝香鐵一らの一連のQC思想を実際の具体的な全体のビジネスプロセスにまで落とすことができたのは、トヨタ本体くらいだと言われています。ほとんどの日本企業では量産工場への初歩的な現場向けQC手法導入で止まってしまいました。当時は99%の日本企業が途上国型の下請製造・コピー/リバースエンジニアリング業の時代。Total QCの”Total”は、ほぼ全ての企業で下請プロセスしかなかった、ということです。そのため本題の「企画の質」「設計品質」の仕組みはよく知られることがありませんでした。書籍があふれ世界中にも広まり今やモディティ化したTPS(国道248号線の西)は最低限の知識。次のステップはTPDを学び世界で勝てる組織をつくること。その際、欧米のTPS+Gemba QCの誤解を含んだ旧式のリーンとその派生モノでは当然限界があります。Sakai’s Qality Creation Dagramで現状の診断・把握とあるべき姿を見える化します。
GET STARTED NOW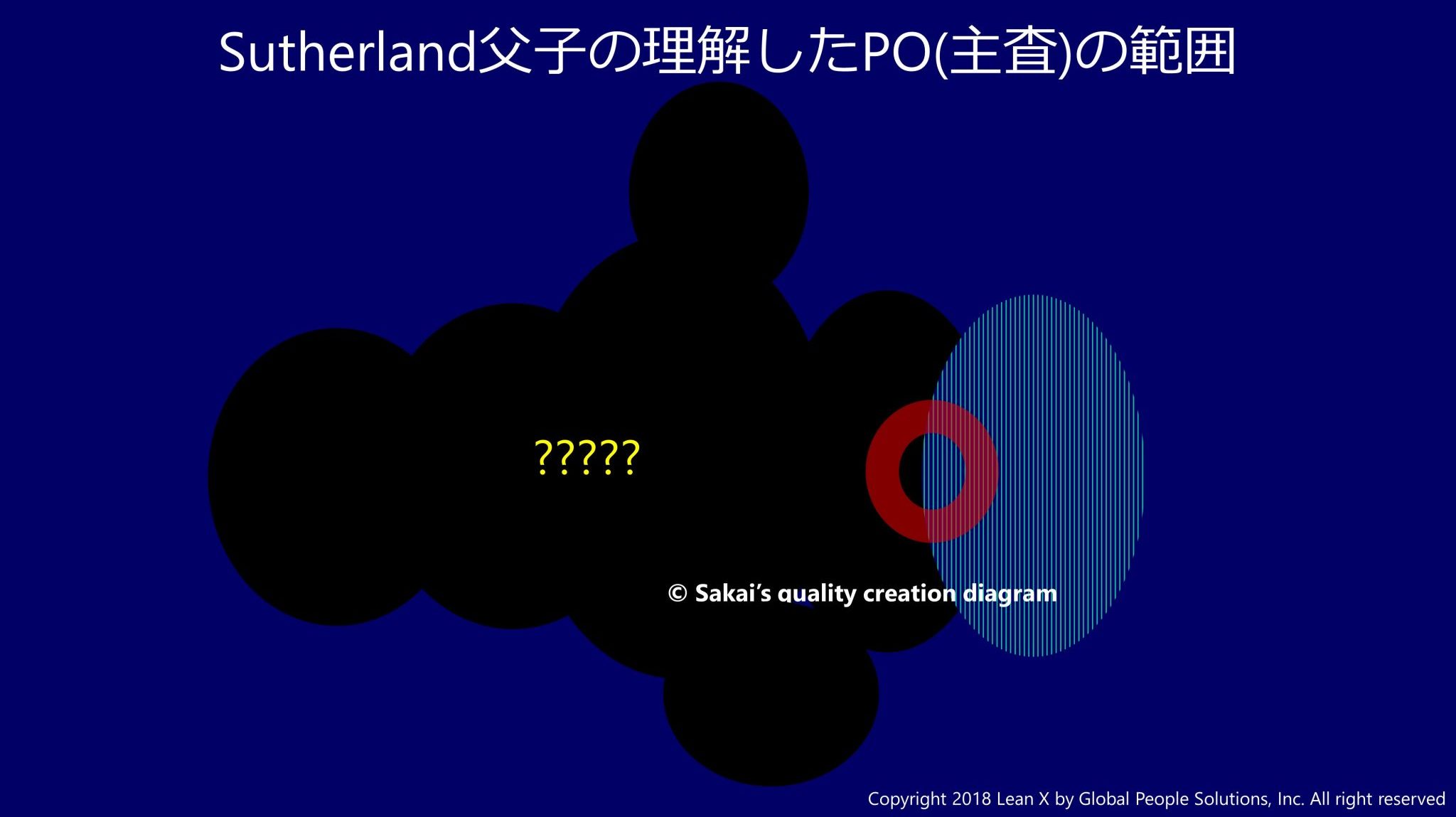
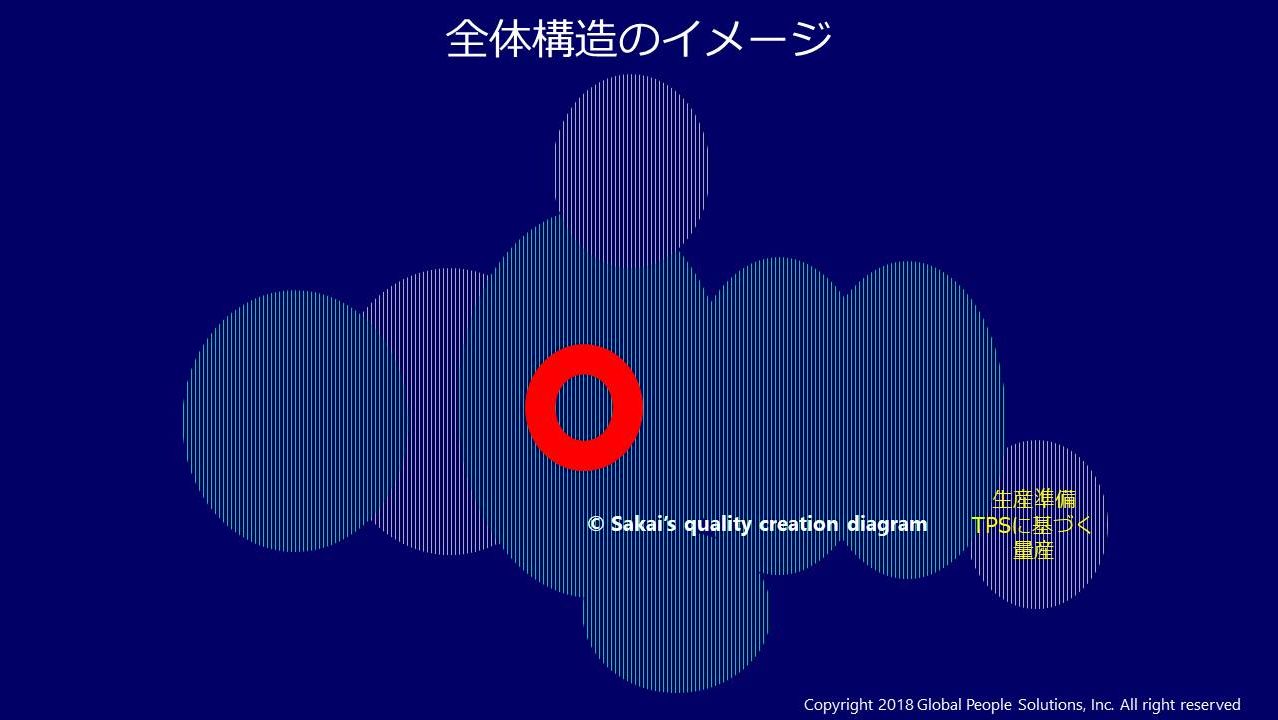
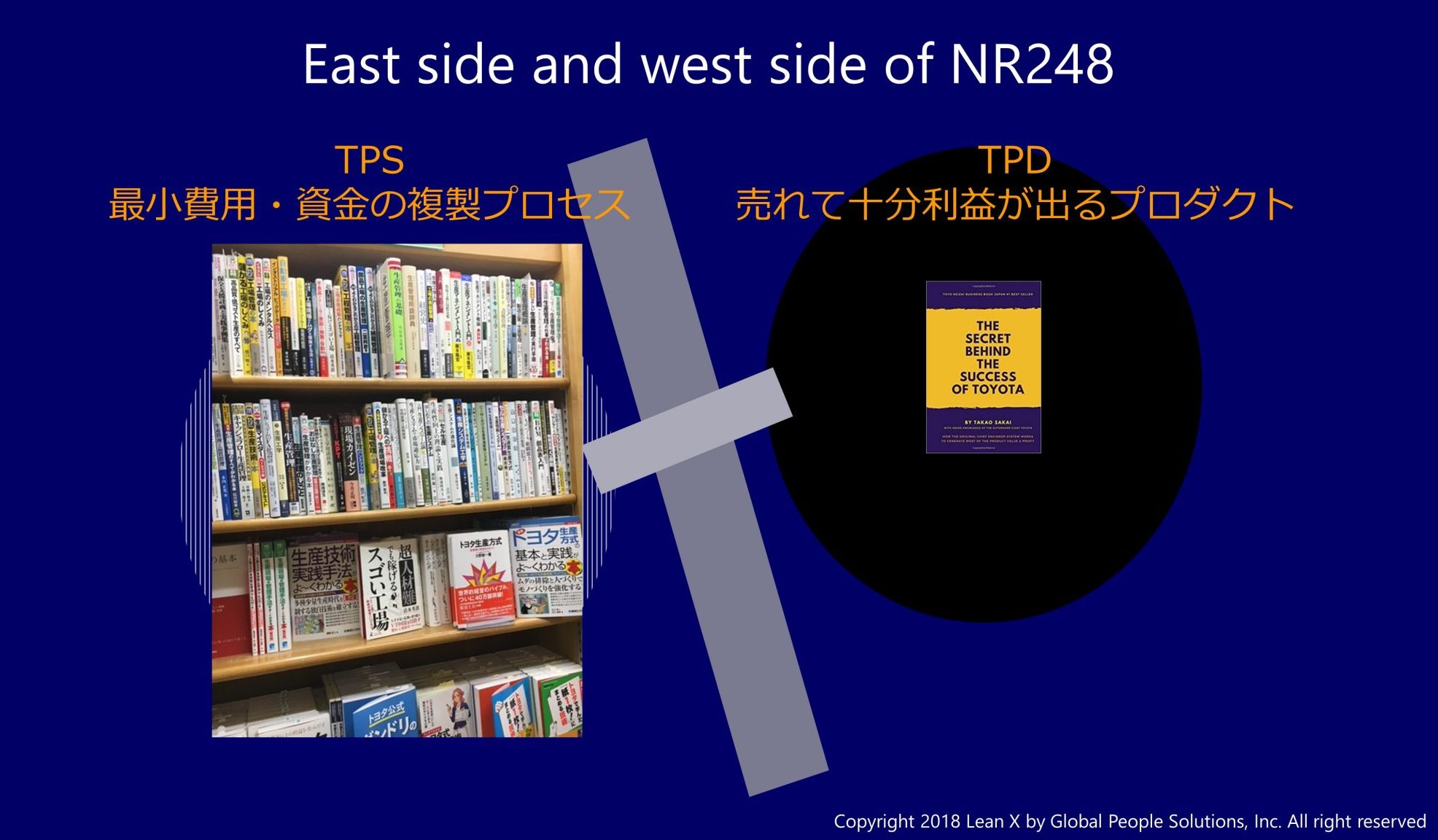
Made in Japanの終わりと日本のこれから
優れた生産技術とTPSといった日本独自の生産管理手法の展開、つまり工場の量産ノウハウ競争の時代は終わりました。TPSはトヨタ本体の国道248号線の西側で発達した手法ですが、現在トヨタは生産の70%弱を海外工場で外国人が行っています。いまはプロダクト&プロセスイノベーションで価値と利益のほぼ全てを生み出す時代。企画の質・設計品質、TPDで勝負の時代。知識を経済価値に換える組織的な仕組みで世界で稼ぐ時代です。
GET STARTED NOW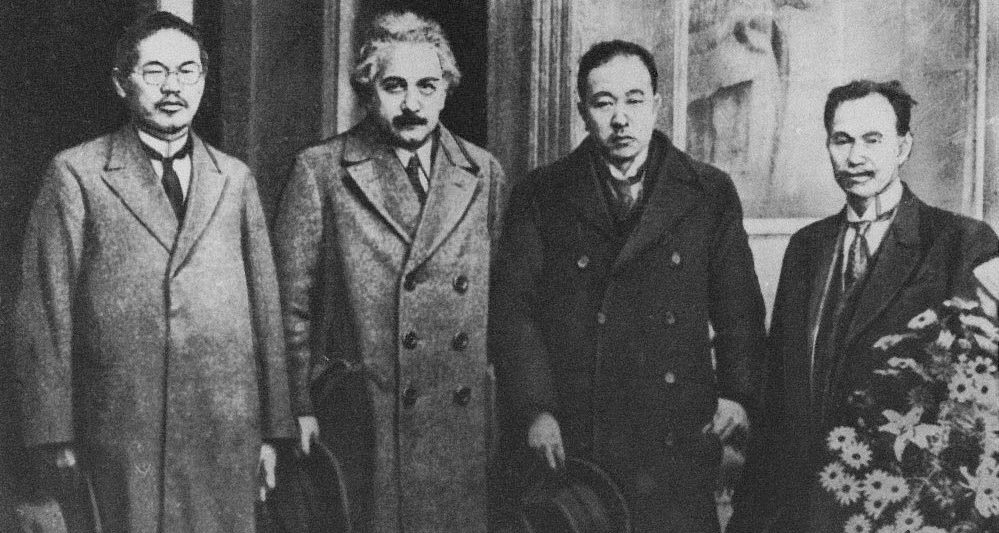
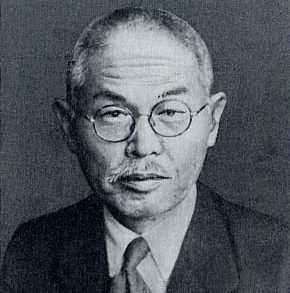
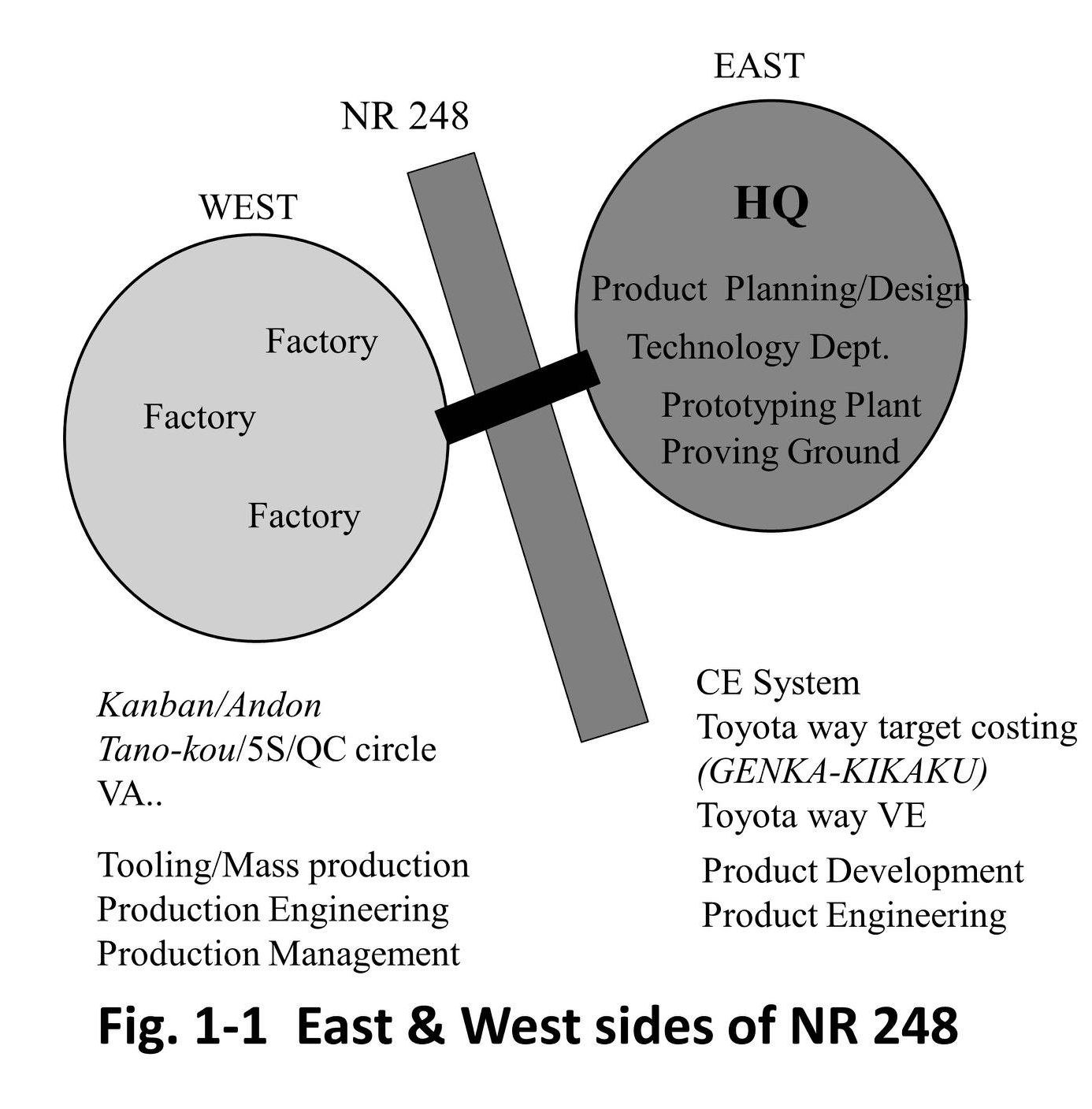
工場発想から売れるモノ開発 。企画の質・設計品質
Made in Japan戦略時代の工場の生産管理ノウハウは世界中で知られています。従来の欧米型旧式リーンは、TPS+GembaQCのこと。世界中で学ばれ、すでに実践されています。人件費の高い日本人は次のステージへステップアップしなければいけません。日本の産業が得意とするべき複雑な人工物(Artifacts)財の創造競争では、TPD以上のフレームワークはまだ知られていません。
GET STARTED NOW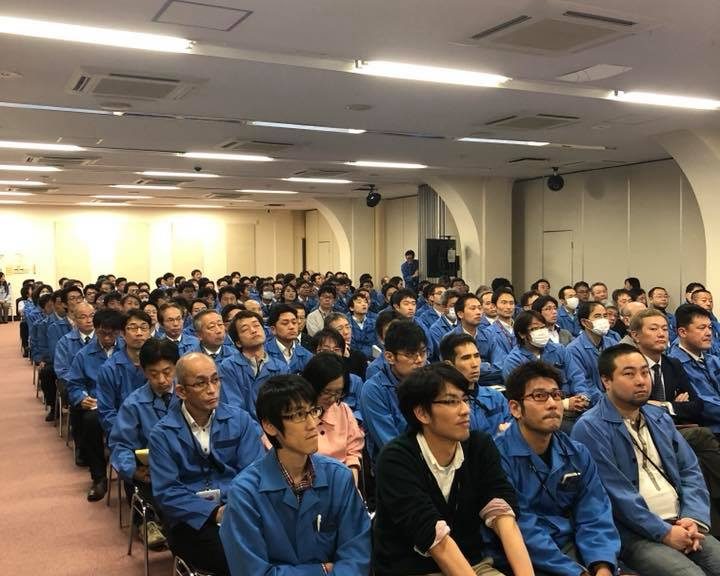
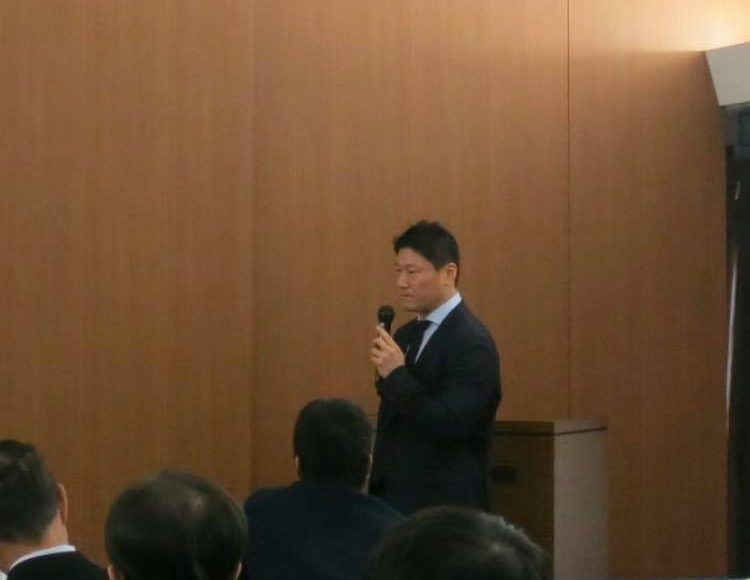
レベルに応じたリーンの導入
とはいえ、医療業界や政府・地方公共団体・外郭団体では、1950-60年代の初歩的なリーン手法すら知られおらず、世界各国共通の典型的なアンチリーン業界とされています。公共・準公共・民間を問わず、今も残る低品質・高価格で不経済な社会問題セクターについては、従来のリーン手法と一部追加のノウハウでサービスを高品質・低コスト化し比較的短い時間で実現していくことができます。 中でも米国・欧州といった先進国では医療費の高騰、社会費用負担が財政を圧迫する深刻な問題となっており、早急な解決が求められています。 もちろん我が国も例外ではない状況。米国・北欧では古典リーンの医療業界への応用であるリーンヘルスケアが積極的に展開され始めています。
日本人の頭と腕で○○産業は確立できる
私の先祖の本多光太郎は80年前田舎のスタートアップの創業者であった豐田喜一郎が挫折し半ば諦めかけて助言を求たとき「日本人の頭と腕で自動車産業は確立できる。外国人に恃む必要はない」と言ったと聞いています。その言葉を聞いて喜一郎は元気百倍三河に戻り、今日に続く自動車産業を確立する礎をつくりました。現在は、先人達の努力によって、喜一郎達の時代とは比較にならないほど多くの知的なノウハウが蓄積され活用できます。今後我が国が伸ばさねばならないIT・ソフトウエア産業・通信・半導体・電機・医療は当然のこと、プロダクト・プロセスイノベーションによって再び世界で勝てる産業を創り出すことは、「日本人の力でもちろんできます」。なぜなら外国人が我々から学ぶ時代となっているからです。
Contact us
講演・ワークショップ・コンサルティングのご依頼はこちらからお受けしています